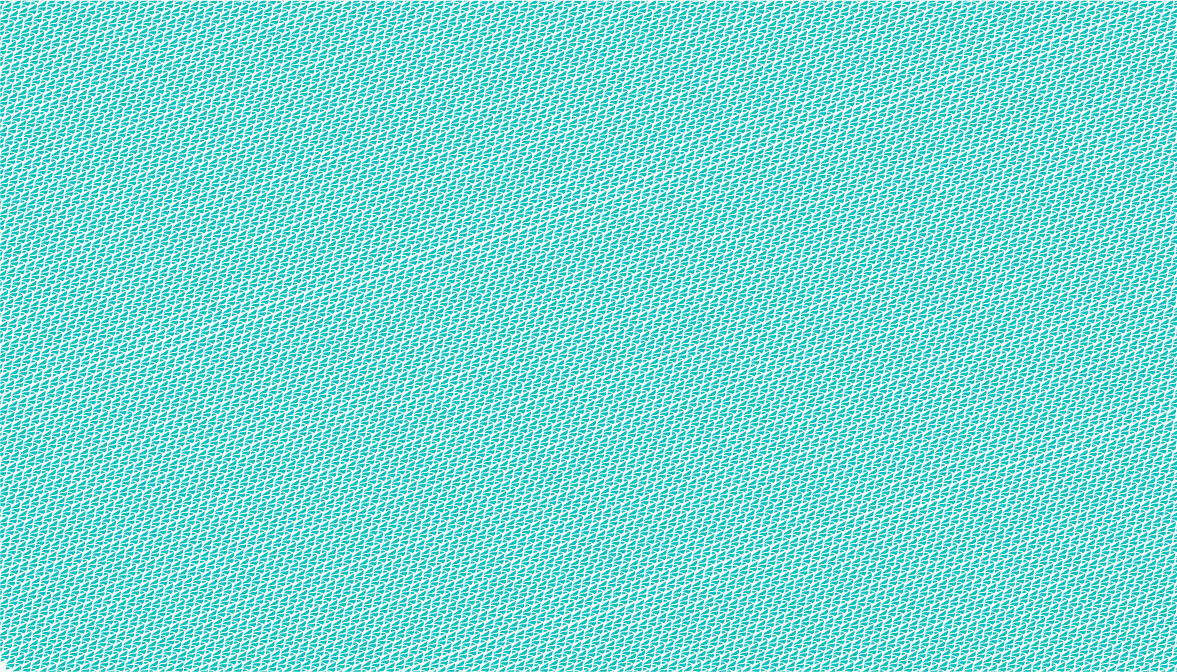
Computational Fluid Dynamics
Computational fluid dynamics (CFD) is a computer-based analysis method that solves fundamental equations of fluid flow numerically within an analysis domain. Many different aspects of fluid flow are able to be examined, resulting in an in-depth understanding of the underlying fluid mechanics. EBDG uses an advanced form of CFD that accounts for fluid viscosity effects including turbulence and flow separation. EBDG views CFD as a powerful component of our design process. Our CFD analysis has guided both physical design as well as the operating conditions of vessels to obtain improved fuel economy for operators.
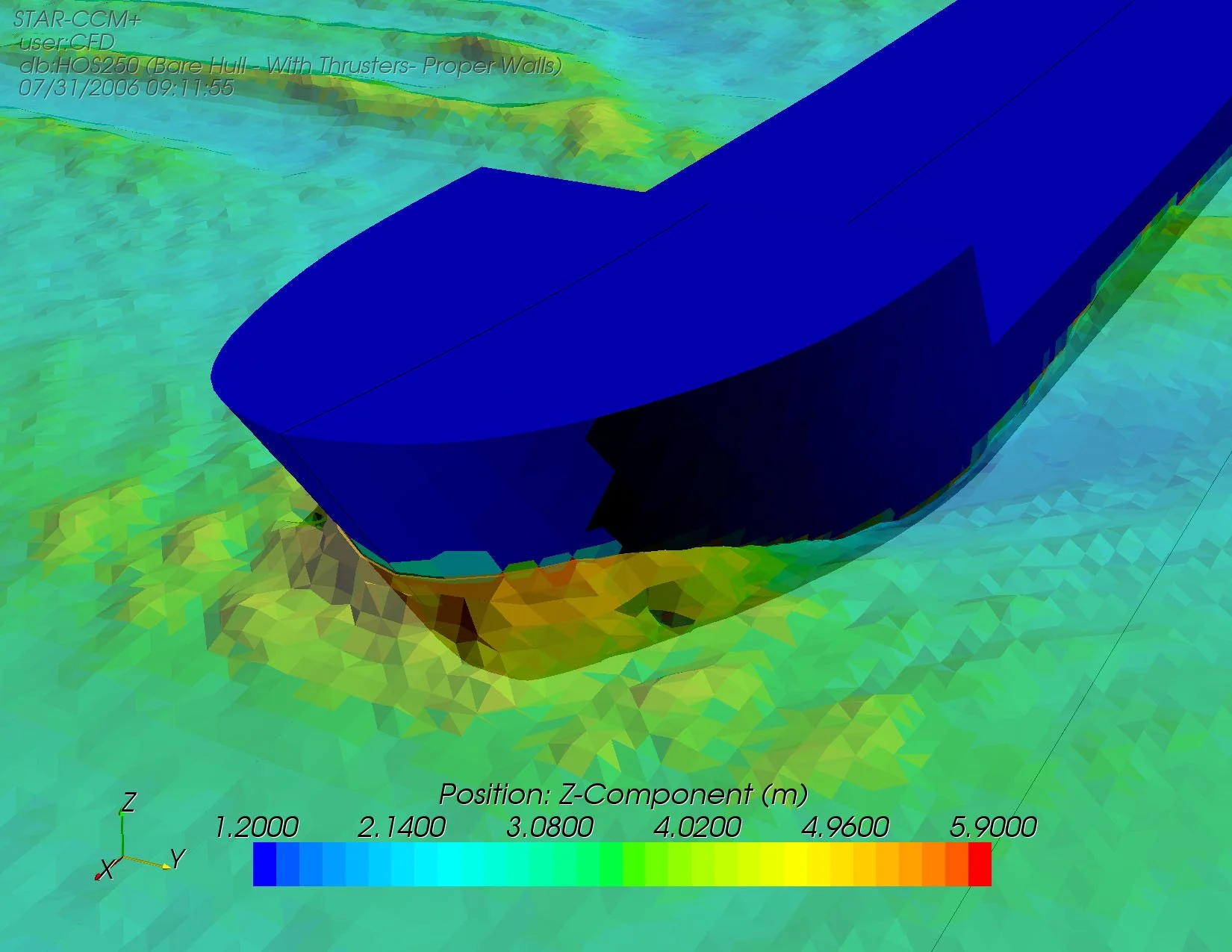
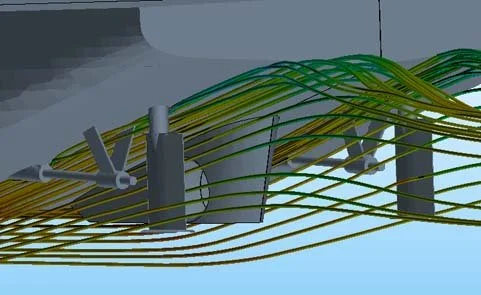
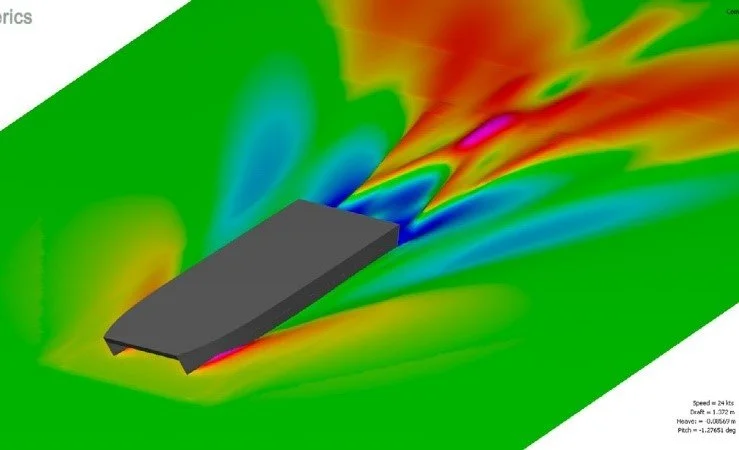

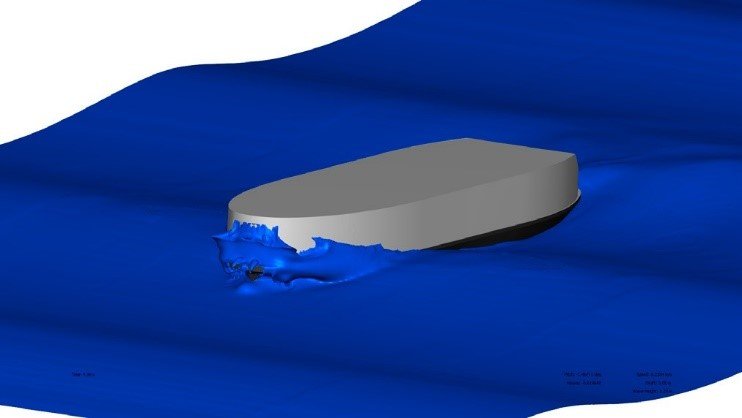
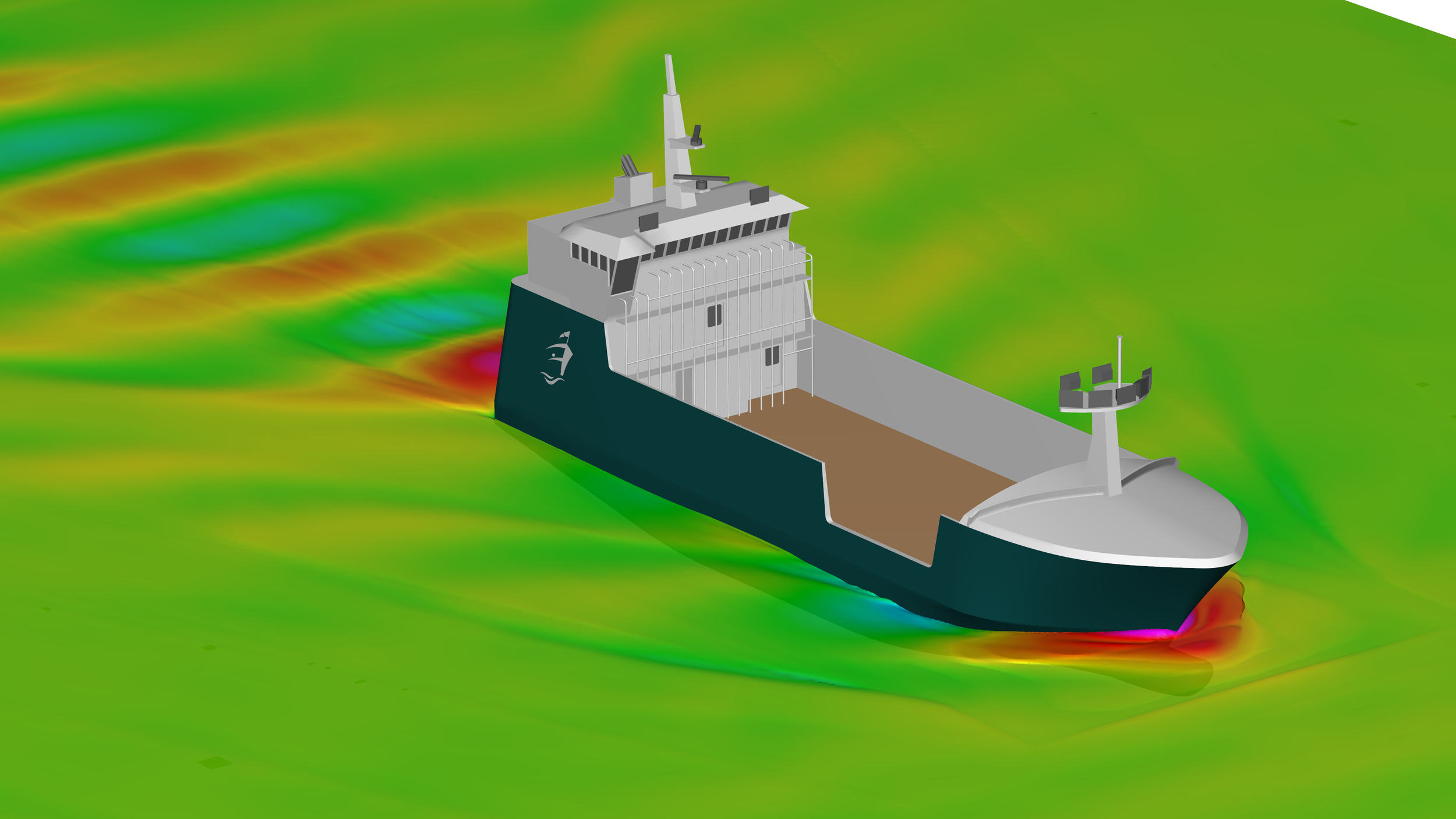


Applications of CFD
Hull Resistance and Appendage Drag Prediction
6 Degree of Freedom Motions
Ventilation and Piping System Performance
Gas Dispersion Studies
Superstructure Aerodynamics
Rudder and Propeller Studies
Exhaust Plume Analysis
Dynamic Vessel Tow Characteristics
Flow Induced Vibration
Vessel Operating Trim Optimization
EBDG Approach
Our CFD strategy is to apply analysis capabilities to both new-build vessel designs and existing structures. With the continual increase in computer processing power and the software to take advantage of multiple processors (cloud computing) we can harness the power of a supercomputer to perform our simulations. And by continually honing our in-house tools and procedures we can efficiently perform advanced analysis with accuracy and speed.
We have applied CFD both as an alternative and as a complement to physical model testing, saving our clients substantial financial resources and time. This approach results in tangible benefits for our clients.
Case Studies
Resistance Analysis
EBDG performed a resistance analysis for a high-speed ferry as part of a project with Sandia National Laboratory. CFD allowed EBDG to determine the planing dynamics and resistance of the vessel with much more accuracy than with traditional parametric analysis.
Time-Domain Seakeeping Analysis
EBDG performed a time-domain seakeeping analysis of the WOODS HOLE for The Steamship Authority. The vessel response in extreme wave events was analyzed to determine if the operating limits of the vessel could be increased. The use of CFD allowed EBDG to accurately examine green water and spray on the bow of the vessel.
Foil Design For A 211 FT Yacht
EBDG designed a foil for adjusting the running trim of a 211ft yacht for Delta Marine Industries. CFD made it possible to rapidly analyze multiple concepts for the foil design. EBDG employed CFD not only to determine the performance of the individual foil, but to examine the interaction between the foil and the vessel to attain a realistic prediction of the vessel performance.
Liquefied Natural Gas Dispersion Study
EBDG studied the gas dispersion pattern for a liquefied natural gas (LNG) fueled tug. The gas dispersion analysis in CFD examined the multi-species mixing effects of LNG venting over a range of wind headings. The flammable limit envelope volume was determined. This allowed accurate placement of the vent stack and hazardous zone definitions on the tug which optimized the arrangement.
In the Media
CFD at EBDG - Watch Now