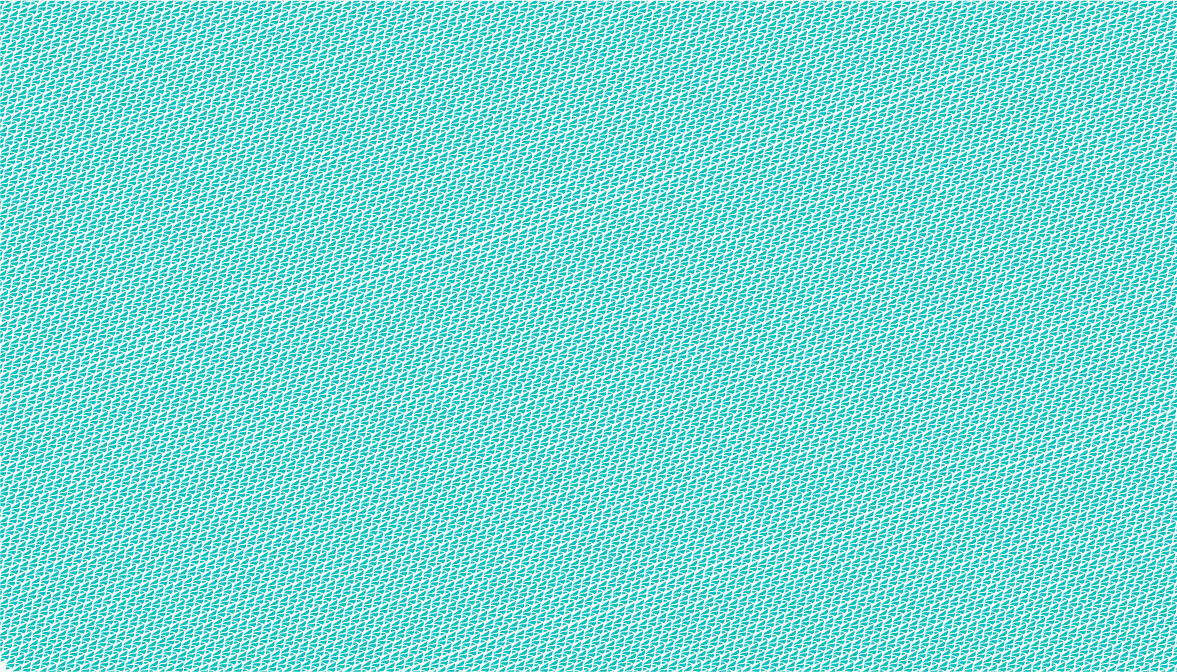
ATB Barges
EBDG offers extensive expertise in articulated tug and barge (ATB) design, covering deck, product, combination, and LNG ATB barges. Our designs emphasize hydrodynamic performance, efficient structural design, and environmentally-friendly systems. We provide full technical and regulatory support through all stages, ensuring seamless engineering, repair, refit, and new construction processes. EBDG’s ATB designs are crafted for optimal operational efficiency and cost-effectiveness, making us a leading choice for innovative ATB solutions.
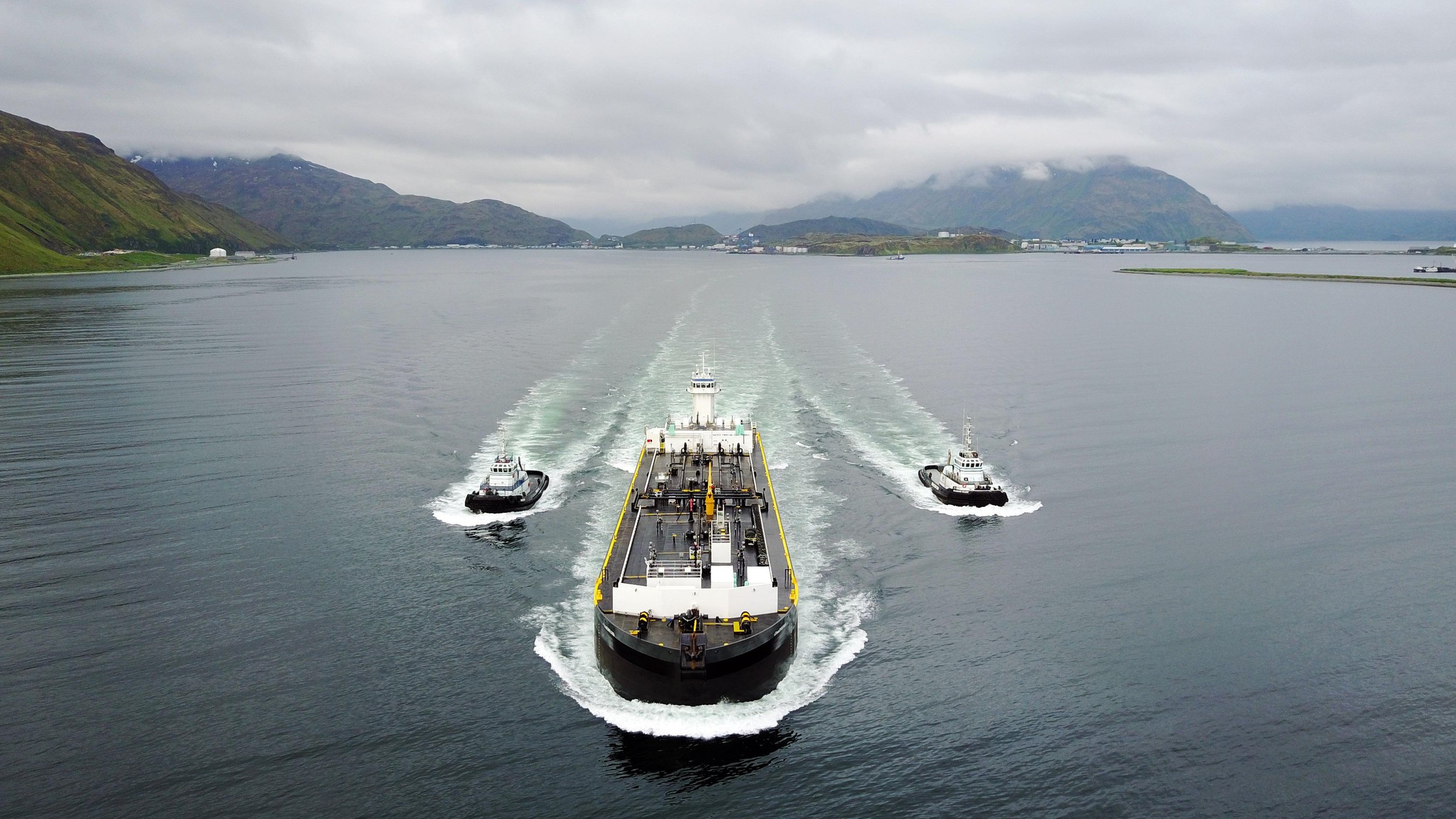
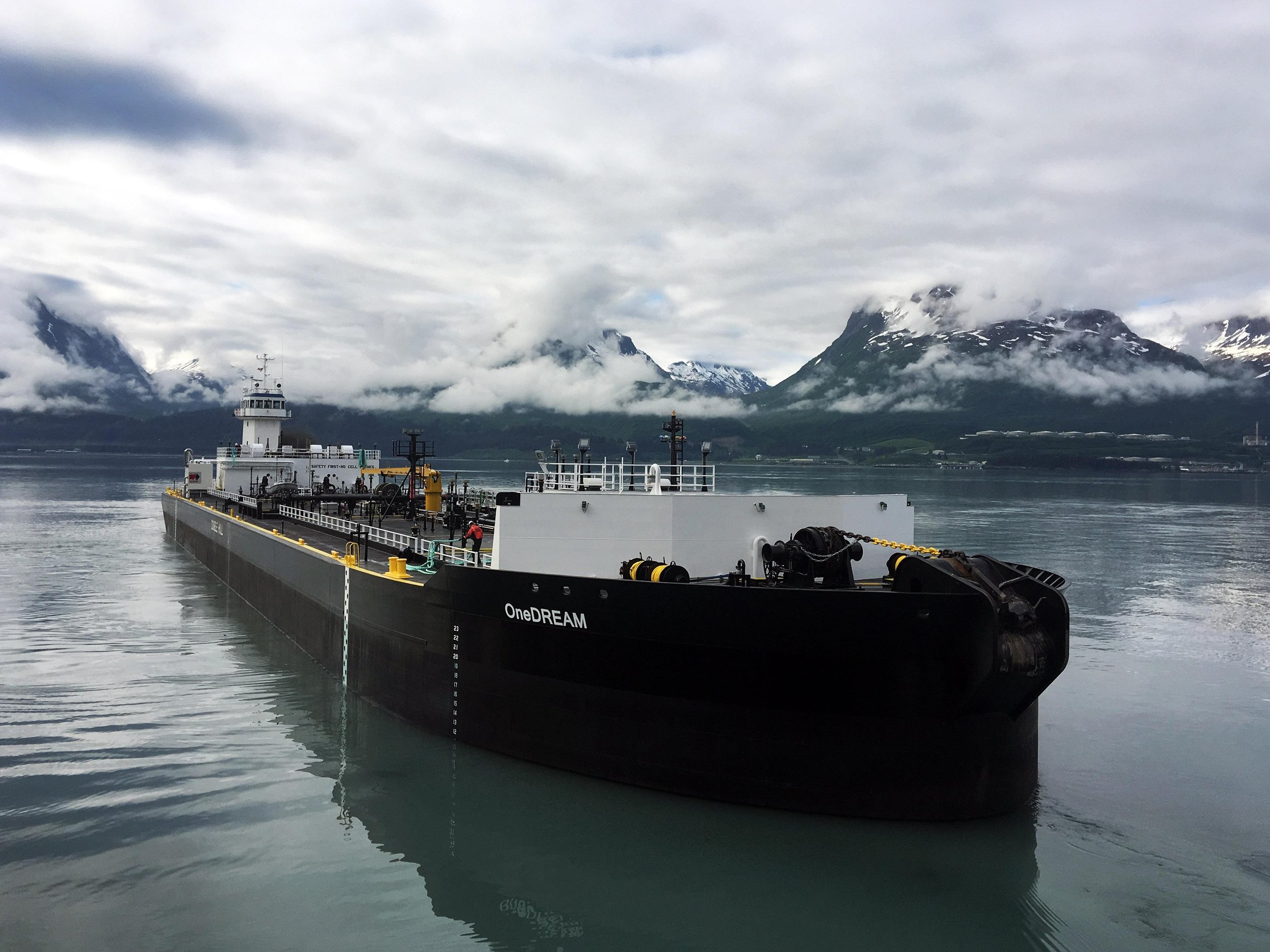
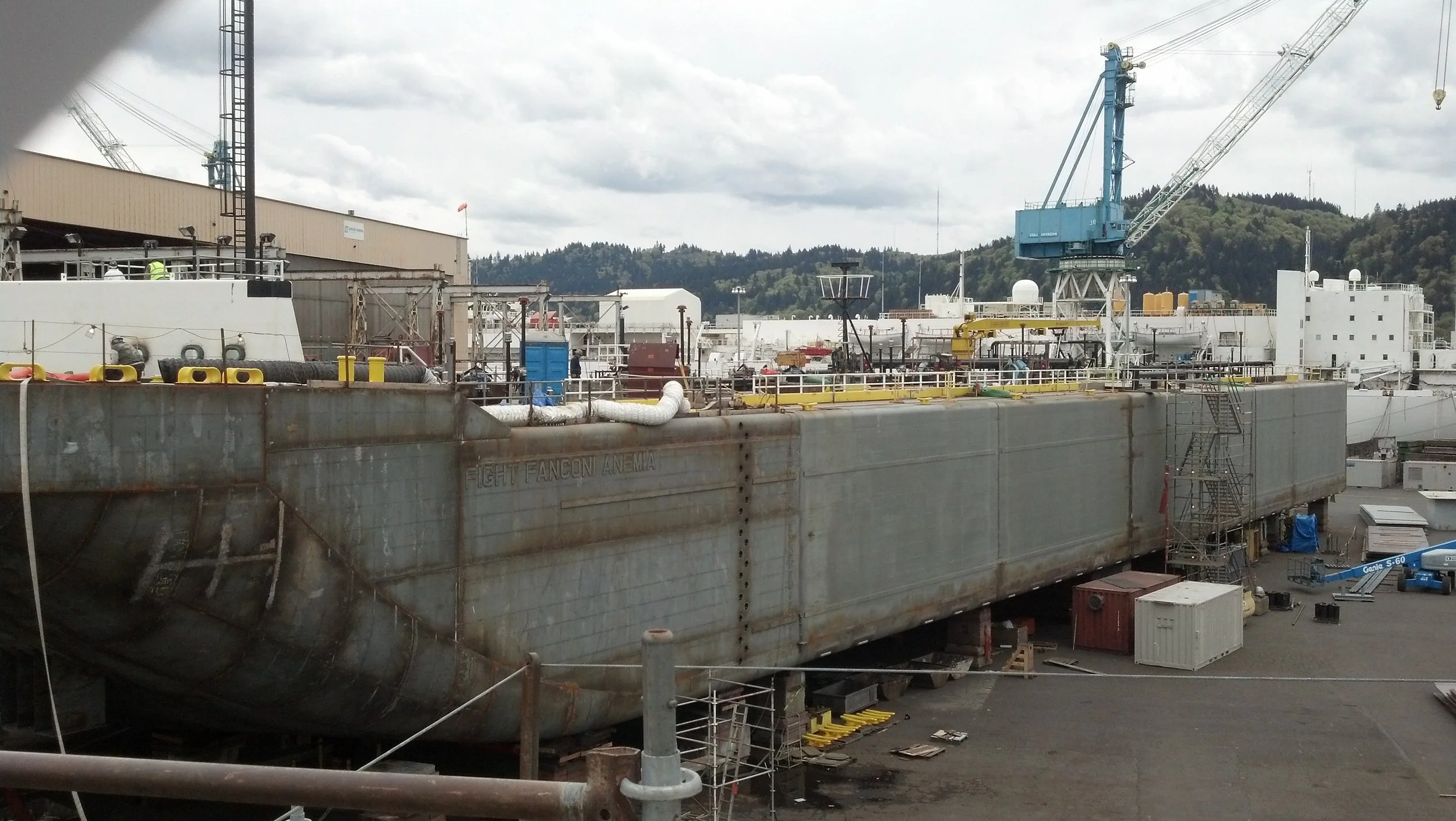



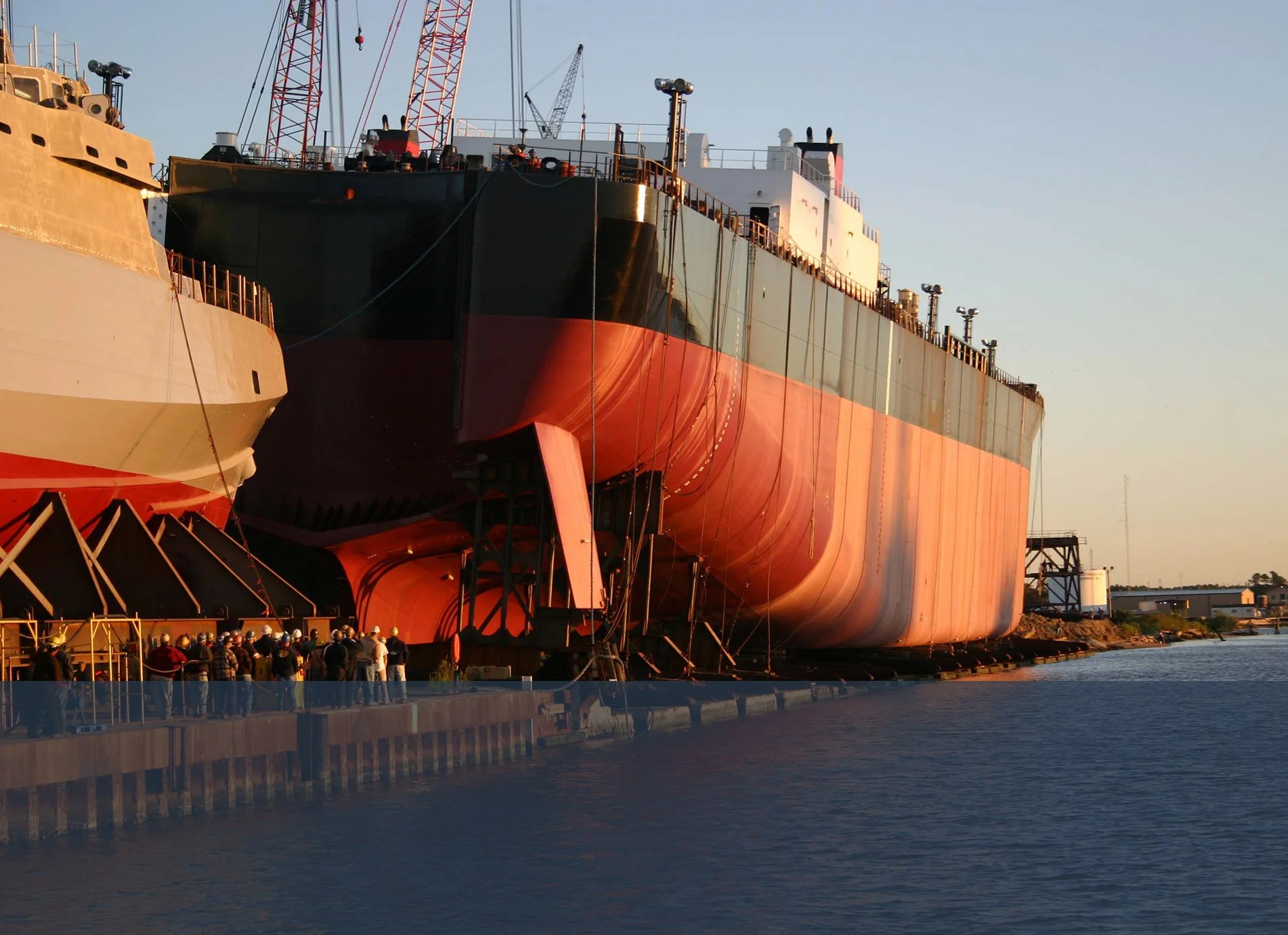


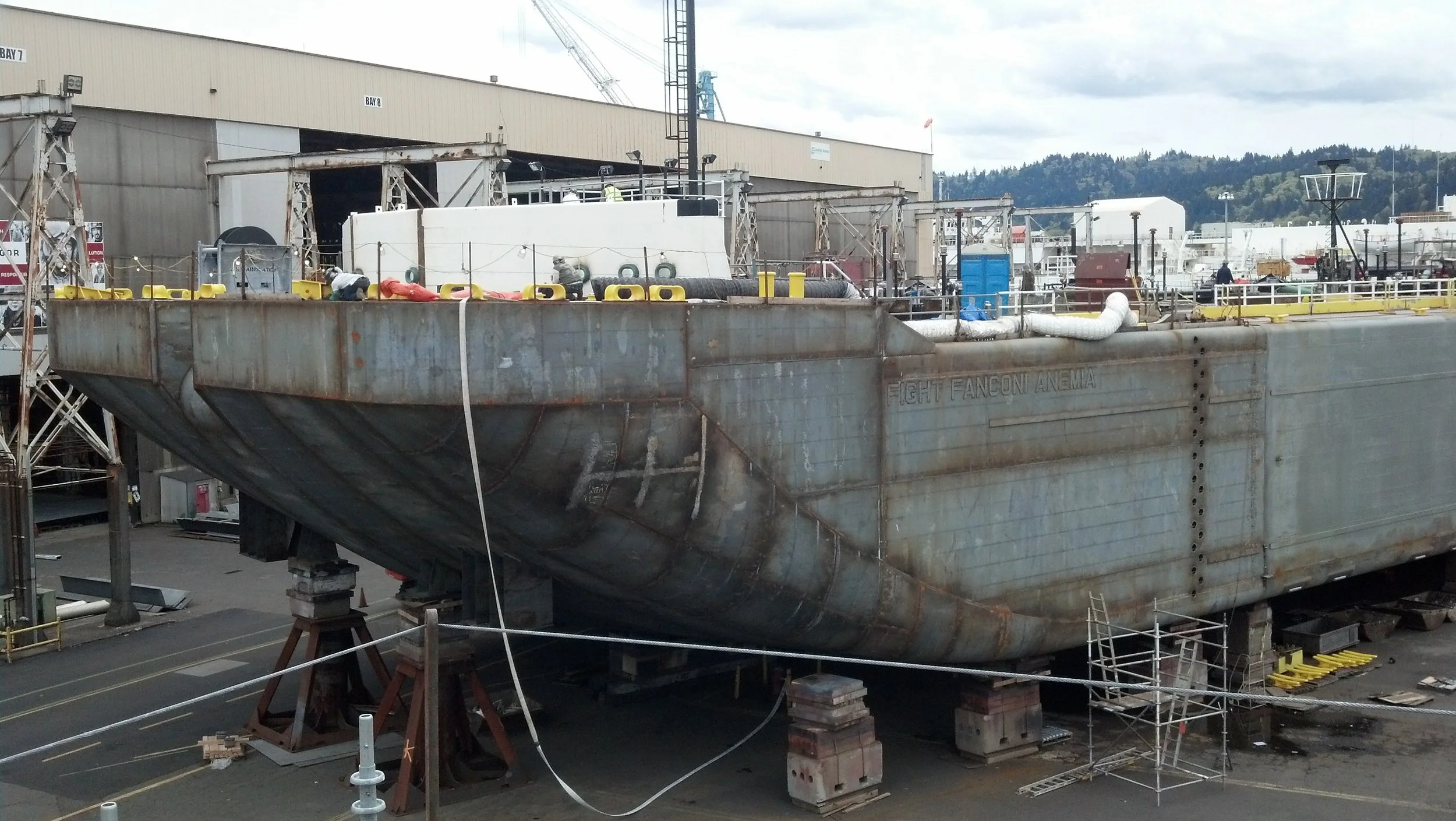



Shallow Draft ATB
Coastwise Engineering provided design, engineering, and construction support for a shallow draft articulated tug and barge set. The unique set of vessels, owned by Brice Marine of Fairbanks, Alaska, is designed to serve remote rural Alaskan communities and construction sites with shallow rivers or bays and unimproved beaches. The 180-foot steel barge, DRIFT RIVER, is a USCG certified subchapter I cargo barge with a stern notch and a Beacon Finland socket plate to fit the ALULAQ’s pin coupling system. The barge is capable of carrying approximately 1,000 long tons of cargo, which can include up to 28,000 gallons of fuel oil for use by the tug during long voyages. The DRIFT RIVER includes a bow ramp for roll on/roll off equipment loading at unimproved beaches.
28,000 BBL ATB
EBDG provided contract design, detail design, and production support for an ATB pairing for Harley Marine Services, now operating as Centerline Logistics. The tug is the 95' DALE R LINDSEY and the barge is the 220′ PETRO MARINER. The barge features an ATB stern rake configuration, segregated cargo tanks, a cargo handling crane, fore and aft anchor winches, and the ability to carry limited deck cargo. The ATB has capacity for 28,000 barrels of cargo.
83,000 BBL ATB Barge
EBDG completed preliminary and contract design of an 83,000-barrel ATB tank barge. The 422' barge features a vapor recovery system with options for cargo heating and tank inerting. The vessel is outfitted with a forward breakwater that protects the anchor and mooring winches. Cargo is stored in 12 onboard tanks and can be loaded at 10,000 barrels per hour. The ATB barge is certified by ABS and USCG to carry Grade A and lower petroleum products. EBDG provided production support and regulatory liaison during barge construction. Several hulls have been delivered to this design and EBDG worked with the client on design modifications over the years to optimize operational efficiencies.
330,000 BBL ATB Barge
EBDG completed a functional design for the barge portion of a 330,000-barrel ATB. The 600' barge has 14 cargo tanks onboard with capacity for 330,000 barrels. The vessel is designed to carry a variety of oil products and will sail under US Flag registry. The project scope included complete design of the structural, mechanical, electrical and outfitting systems. EBDG performed the engineering necessary to obtain regulatory approval of the design, including the SafeHull A and B calculations and other finite element (FEA) analyses. ABS Safehull and FEA tasks included scantling modeling and first principal analysis iterative design, strength modeling and FEA assessment, Thermal Strength FEA and Stern Notch and Connector FEA.
This ATB barge design has been modified three times for specific client operations. One of the design modifications included a stand-alone deck house for inert gas machinery, pollution control systems and cargo heating systems. Three hulls have been built to this design.